General details
EDIHs involved
Customer
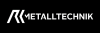
Customer size: Small (10-49)
Customer turnover: Annual sales: 2 700 000 Euro
Challenges
RK Metalltechnik is a versatile contract manufacturer specialising in sheet metal processing. They offer customised solutions for small batch sizes with a delivery time of just 5 working days. Services include laser cutting, edge rounding, bending, welding and mechanical processing. When unloading the laser cutting system, employees have to clear parts quickly. In order to further improve competitiveness and further reduce delivery times, the aim of the project is to determine whether a spatial augmented reality system can support this. Specifically, it is about the technical feasibility of an active visualisation for a better understanding for the machine operator through projection directly on the sheet metal parts including the necessary interfaces in the digital process chain. This involves assessing the technical feasibility of an active visualisation system that projects information directly onto the sheet metal parts, aiding machine operators in better understanding and quickly managing the unloading process.
Solutions
The solution deals with the integration of active projection technology based on a multi-projector setup in manufacturing to enhance the efficiency of unloading and order picking from the cutting table. This innovative solution ensures parts are directly loaded into customer containers with greater accuracy and speed.
Key aspects of the solution include:
-
Active Visualisation: Utilising projection technology, colored highlights and essential information are displayed on the cutting table, guiding operators on part selection and sequence.
-
Technical Feasibility: A detailed analysis confirmed the technology's integration with existing machinery and its capability to accurately project necessary information.
-
Digital Integration: Adjustments in the digital process chain were made to ensure the projection system received order data, enabling dynamic operator guidance.
-
Laboratory Demonstrator: A proof of concept was developed in a controlled environment, testing the system's practicality and effectiveness.
-
System Integration Evaluation: The concept's compatibility with existing systems was thoroughly assessed, ensuring seamless operational enhancement.
This implementation significantly improves parts handling efficiency and accuracy, showcasing the effective combination of traditional manufacturing processes with advanced digital technologies for optimised performance. By leveraging multi-projector setups and real-time guidance systems, this solution enhances operator productivity and minimises errors during the unloading and order picking process. This transformative solution not only streamlines operations but also showcases the potential of innovation to drive tangible benefits in productivity, quality, and customer satisfaction within the manufacturing industry.
Results and Benefits
-
Digital Interface Enhancement: The projection system acted as a digital interface between human operators and machinery, effectively expanding the existing CAD/CAM process chain. This integration facilitated faster order picking, contributing to a noticeable reduction in delivery times.
-
Workload Reduction for Employees: By providing a clear, visual guide for part selection and placement, the system significantly reduced the cognitive and physical workload on employees. This led to a more streamlined and less error-prone process.
-
Elimination of Paper-Driven Processes: The projection technology eliminated the need for paper-based processes and reliance on fixed displays. Operators received real-time, projected information directly on the components, detailing clearing orders and the necessary picking process for each order.
-
Equipment and Development Scope Derivation: The project successfully outlined the necessary scope of equipment (both hardware and software) and the developmental efforts required for a pilot system in a real-world environment.
Through these advancements, the projection system not only improved operational efficiency but also enhanced the working conditions for operators, marking a significant step forward in integrating digital solutions into traditional manufacturing settings.
Perceived social/economic impact
This AI-driven digital skills project can have a broad societal impact, affecting various aspects of life. It could help to bridge or narrow the digital divide between urban and rural areas, or between socio-economic groups, offering AI-based training to women, minorities, and people with disabilities.
As AI and automation reshape the job market, this digital skills project can upskill workers, making them more employable in tech-driven fields such as data science, machine learning, and robotics. This helps to maintain a competitive workforce. AI tools help small businesses operate more efficiently. By fostering AI skills, individuals may be encouraged to innovate and create startups, contributing to local and global economies. Traditional jobs are being automated, which may lead to job displacement, therefore enhancement of digital skills can help reskill workers, reducing long-term unemployment. With AI advancing rapidly, this digital skills project can foster a culture of lifelong learning, encouraging employees to continuously adapt and upgrade their skills throughout their careers.
A digitally skilled workforce will promote more remote work, digital collaboration, and innovation in workplace culture, reshaping traditional job settings. AI skills projects may lead to innovations that address climate change, improve energy efficiency, and reduce environmental degradation, furthering societal sustainability efforts. AI digital skills projects can promote international collaboration, enabling individuals from different countries to work together on global issues like health, education, and climate change.
Measurable data
Clear Benefit for the company:
-
30% less working time
-
Reduction of error rate to almost zero
-
Support and relief for employees
-
Increase in efficiency
-
Well-being of the workers has been greatly improved
DMA score and results - Stage 0
The average overall Digital Maturity Level of the company at T0 was 36%. The breakdown for each of the dimensions was:
-
Digital Business Strategy: 50% average
-
Digital Readiness: 49% average
-
Human-Centric Digitalisation: 46% average
-
Data Governance: 38% average
-
Automation & Artificial Intelligence: 0% basic
-
Green Digitalisation: 35% average
Lessons learned
-
Importance of User-Centric Design: Tailoring technology to meet operator needs is crucial for successful integration and adoption.
-
Seamless Integration is Key: Harmonising new technology with existing processes ensures minimal disruption and maximises efficiency gains.
-
Continuous Feedback Loop: Regular input from end-users, like machine operators, is essential for refining technology applications in real-world settings.
-
Evaluating the projection system at the target facility is a valuable approach, as it allows for real-time assessment and adjustment in the actual working environment, ensuring the technology meets specific operational needs effectively.
Other Information
Industry 5.0:
The working atmosphere at this machine has improved drastically! There is less stress for the employees now. They didn’t know that the unloading was such a big issue for the workers!
Due to digitalisation in this process step the wellbeing of the workers has very much improved. And here we are talking about Industry 5.0, because this is a very important aspect of human-centricity.
Employees now feel more comfortable and enjoy operating the machine.
That is what exactly we want to achieve with our hub and we are on a good way.
The company would not have considered this technology without the EDIH service!
Need support?
Consult our catalogue to locate the Eupopean Digital Innovation Hub nearest to you and accelerate your company's digital transformation.